Electrolytic Etching of Brass
Update: I'm often asked about the thickness, type, and source of brass I used for these journals. I am very lucky to have a local place, Metal Source, were I buy most of my supplies. I used 22 ga. (.025") brass and any alloy will do. In a pinch you can buy brass door kick plates at your local home center, but you will need to strip the lacquer. If you can't find any local source you can buy online, but this is the most expensive option.
A while ago I saw Mark Frauenfelder's limited edition Moleskin notebooks on BoingBoing and immediately thought of using the electrolytic brass etching process that I've been experimenting with to make some similar notebooks to give as gifts this year.
As you can see they came out quite well and the Moleskin's two century history lends the project a certain Steampunk street cred.
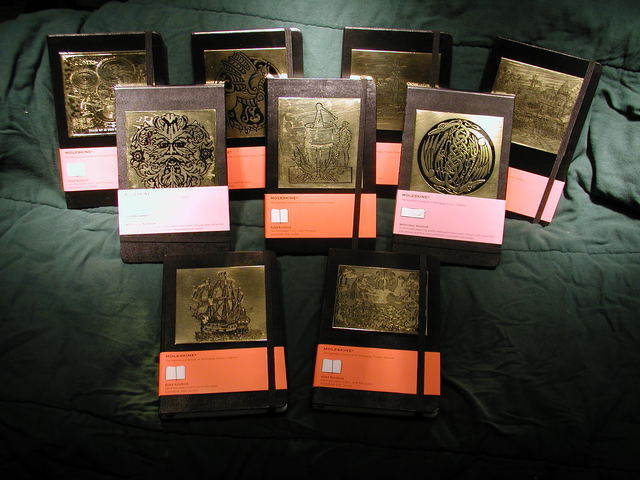
This is a technique I adapted for easily impressing images into brass plate. I say "impressing" but what I'm actually doing is electro-chemically etching the brass. Here's the process:
First we use a laser printer to print a negative of our image onto a sheet of inkjet glossy photo paper. Yes, I did say inkjet paper, this is an "off schedule," use as they say in the pharmaceutical biz.
Next we throughly clean a piece of brass with Scotch Bright and then scrub it with alcohol until it's completely clean. Several alcohol scrubbings will be needed to remove all of the dirt.
Next we use an iron set to it's highest setting to melt the toner onto the brass plate. Press hard on the iron and move it around a bit. I used the roller pictured to further press the paper against the brass. Total heating and rollering time was about 2 minutes.
Once you are satisfied that the toner has been completely melted onto the brass, drop the plate into a tray of hot water. The water soak is intended to soften the inkjet photo paper backing so that it can be peeled away from the toner now stuck to the brass.
This is actually a technique that has been developed by hobbyists for making electronic printed circuit boards. Please see the bibliography below for the source and for more detailed information on this part of the process.
Once the board has soaked for 5-10 minutes, take it out and gently try and peel back some of the now softened paper. After peeling off a layer, return it to the water.
Once you get most of the paper off you can us a stiff brush to remove the remainder. You want nothing left but bare brass and toner.
Now we come to the neat 19th Century technique called Galvanic Etching. You may be familiar with the technique of electro-plating, where a metal object is plated with a layer of another metal by placing it in a bath with a source of plating metal and running current through it.
This is exactly the same thing except we connect our piece to the positive terminal because we desire to remove material from it. This technique was developed in the 19th Century for creating etchings and is still in use today. Again, please see the bibliography for resources.
My research indicated that a copper sulfate solution could be used for etching both copper and zinc plates. Since I wanted to etch brass and brass is an alloy of copper and zinc, this should be the right solution for this project.
A little poking around in the garage and I found this container of "Root Kill" which is essentially all copper sulfate. I mixed about a pound of "Root Kill" into the water you see below. All of it dissolved so I probably could have mixed in a bit more. According to the sites I found, the more saturated the solution the faster the etch.
I made the holders for the brass plates out of brazing rod. I was aware that brazing rod is typically bronze and was hoping that the tin wouldn't mess things up.
The work piece is connected the the positive side of the battery. I used a 12 volt 17 amp hour lead acid gel cell, but a car battery, battery charger, or modified PC power supply will also work. A lamp in series can be used to limit the current flowing through the electrolyte but I found that for the electrolyte I was using and the size of my plates it was not needed. Also, since I want a deep bite into the brass, I don't really need to be gentle.
After a minute or so nothing much was happening, though a brownish residue was forming on the work. I removed the light bulb from the circuit and moved the plates closer together. At this point the 16 gauge power cord I was using started to get warm and I could see the less dense hot water rising around the plates in the bath. I estimate that the current was between 10 and 20 amps. There were surprisingly few bubbles.
At this point things started happening more quickly. I took the plate out of the bath about every 15 minutes and brushed the brownish crud off. After about 45 minutes in the bath I noticed that some of the toner came off while brushing, so I took the plate out and rinsed it well. I used paint stripper to remove the toner but in another test I used steel wool under running water and that worked just as well.
Here is the finished plate, I estimate the bath etched down about .5 mm into the brass. The material removal is very consistent and the lines where the toner was are sharp and clear.
I sprayed the plate with black primer, let it dry, and used sand paper and Scotch Bright to remove the primer from the high spots. Finally, I polished it with some Noxon Metal Polish.
Here's a shot of the finished plate compared with the laser printed negative, you can see that the image is reproduced in the brass almost perfectly.
Below is another test plate that I made earlier, you can see that the lower right sword hilt is missing. This part of the image had been drawn in with a Sharpie and the ink apparently did not hold up to the solution. However, on the back you can clearly make out Charles Babbage's Difference Engine. I had ironed on that toner from a sheet of laser printable overhead film and had rejected it as not leaving a dense enough layer of toner on the brass, perhaps I'll re-visit that technique as it was very easy and fast and clearly has some efficacy.
A Note of Warning: There are some elements of this project that are dangerous and which this article does attempt to address in detail. However, Greenart has extensive information on this process and I urge anyone who plans on trying this to go there, read, and understand the detailed safety and disposal information. In particular you need to read the page on the Bordeaux Etch process as it covers the necessary steps for proper disposal of the spent solution. – Jake.
Bibliography:
Gootee, Thomas P. Easy Printed Circuit Board Fabrication – Using Laser Printer Toner Transfer, http://www.fullnet.com/u/tomg/gooteepc.htm.
Green, Cedric. Green Prints -Etching without Acid, http://www.greenart.info/galvetch/contfram.htm
I just tried your method and I’ve got something strange happening, the photo paper actually stuck to my iron! First time trying this with Inkjet Photo paper, any ideas?
Same thing happened to me. I wonder if it is dependent upon the brand or type of the photo paper.
Take a look at this article: http://steampunkworkshop.com/etching-tins-salt-water-and-electricity-compliment-steampunk-bible-article/
The method describe works better and is way cheaper than photo paper.
It occurs to me that the peeling off of the paper before etching may be an unnecessary step. Electricity should etch the metal through solution-soaked paper with no trouble.
See the link in the comment above, I think it will help.